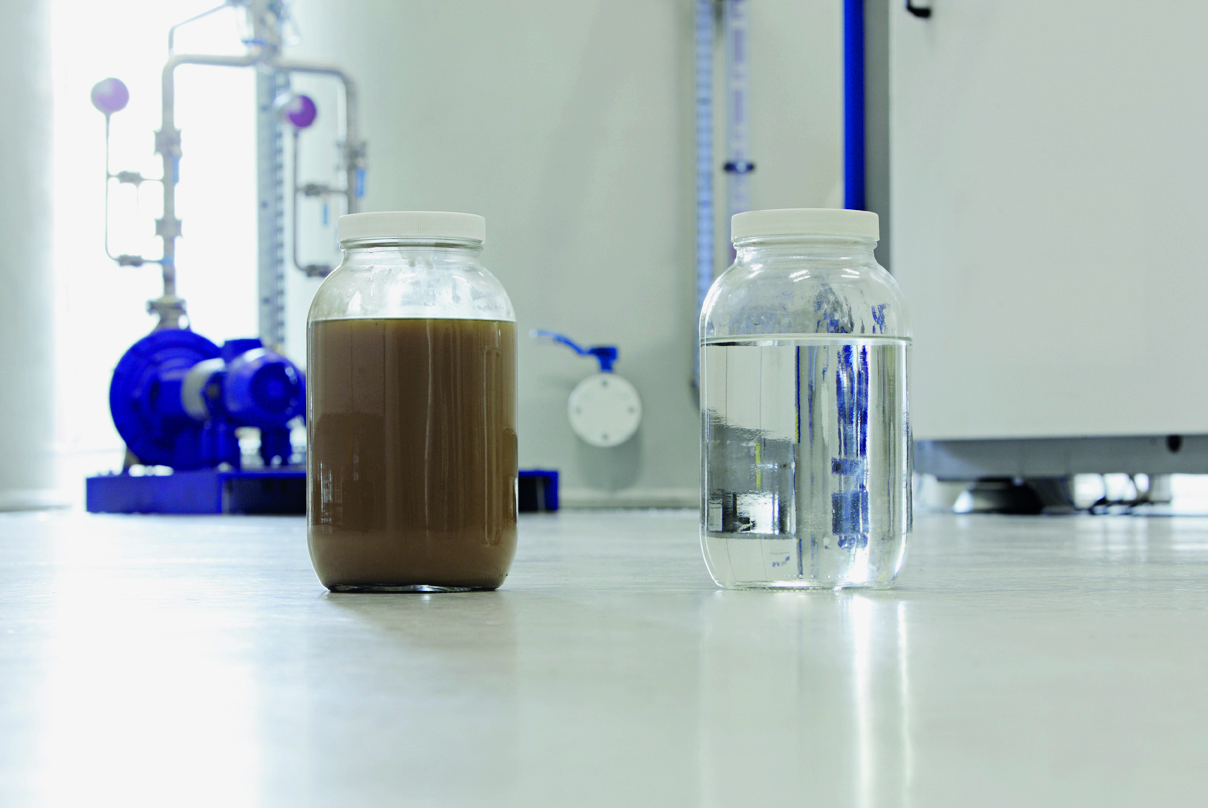
Introduction
Mechanical Vapour Recompression /Vacuum Evaporation Plants for the treatment of emulsions and oil-containing wastewater offer a viable alternative to the disposal of spent coolant and other oil-containing wastewater. This state-of-the-art processing technology allows for the reuse of distillate for preparing fresh emulsions, other workshop purposes, or disposal into the public sewer.
In metal processing workshops, various oil-containing wastewater streams are generated. Emulsions used in different processing technologies contain oil, wax, fat, preservatives, and other ingredients that enhance product properties. These spent emulsions are often disposed of at high costs, typically starting from 150 m³ per year. Mechanical Vapour Recompression/ vacuum evaporation can feasibly process such waste emulsions, resulting in significant cost reductions in the disposal. Typically, return on investment (ROI) periods of less than 2 years are achieved.
Advantages of the VACUDEST Clearcat technology compared to common evaporation plants.
• Undercut legal limits for disposal into the public sewer regarding carbohydrates without post-treatment of
• the distillate in all cases up to now
• Reduction of COD by 98.2 % on average*
• Excellent distillate quality, free of germs, free of heavy metals, almost free of salts
• Low running cost
• Simple, reliable process
• Is applicable for changing emulsion compositions.
• Lowest amounts of residues, thus lowest disposal cost
* Statistical average based on a field study of the H2O GmbH. The COD reduction depends on the chemicals used.
The distilled water leaving the vacuum evaporator can be reused in the workshop, for example, in producing new emulsions or disposed of into the public sewer. Both options require excellent water quality. Traditional evaporation systems may carry significant amounts of hydrocarbons and free oils into the distillate, necessitating post-treatment with coalescence separators, active carbon filters, or membranes to meet legal disposal limits or internal reuse quality standards. The innovative H2O Clearcat technology eliminates the need for additional process steps by allowing the separation of dissolved hydrocarbons and free oils. The resulting distillate is crystal clear and virtually oil-free, eliminating the need for further treatment before reuse or disposal. Introduced since the beginning of 2007, the H2O Clearcat technology has been installed in more than 50 plants, showcasing its practical effectiveness. The technology has exceeded expectations in terms of distillate quality and COD reduction compared to common evaporators, resulting in significant cost savings and compliance with strict disposal regulations.
Commitment 1
Crystal Clear Distillate The H2O laboratory has thoroughly examined over two dozen distillate samples from various VACUDEST Clearcat evaporators, with a similar number of samples independently analysed by end-users. In stark contrast to distillates from standard evaporators, which often exhibit significant milky turbidity and contain free oils, all Clearcat distillates have consistently been colourless, clear, and devoid of any noticeable turbidity. Moreover, no costly post-treatment is necessary; these distillates can be immediately reused.
Commitment 2
Oil-Free Distillate According to DIN ISO 9377-2 Every sample demonstrates remarkably low carbohydrate values, significantly undercutting the strict legal disposal limits outlined in the German water resources law. Notably, even the anticipated future limit of 5 mg/l in France has been consistently surpassed in all instances. The carbohydrate reduction in the distillate has reached up to an impressive 99.9%.
Commitment 3
Commitment 3: Additional COD Reduction of Over 25% in the Distillate Compared to Standard Evaporation Plants Without Clearcat Technology To validate the additional COD reduction, an extensive field study was conducted, examining the total COD reduction. All samples were sourced from VACUDEST Clearcat evaporators installed across metal processing workshops throughout Europe. The results were beyond expectations, with the average COD reduction achieved by the VACUDEST Clearcat technology reaching an impressive 98.2%. This represents a substantial improvement of 63% compared to standard evaporators. Consequently, even stringent COD limitations for disposal into public sewers are often comfortably met in industrial settings without the need for post-treatment. For instance, one notable example includes the COD reduction in a coolant emulsion from 50,000 to 200 mg/l in the distillate.
Conclusion
In conclusion, the Clearcat technology represents a new standard in treating oil-containing wastewater, offering unparalleled distillate quality, reduced operating costs, and simplified processes.