Case Studies
Efficient wastewater treatment for efficient engines
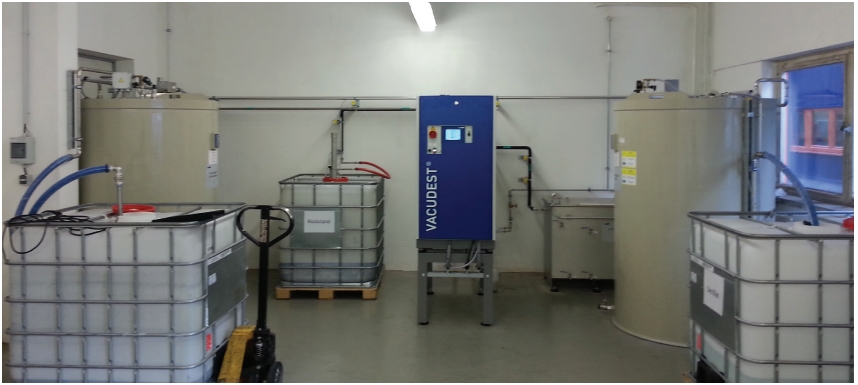
Efficient wastewater treatment for efficient engines
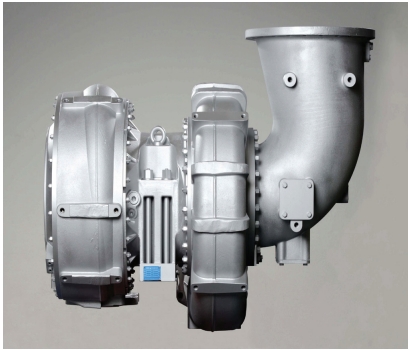
Kompressorenbau Bannewitz GmbH (KBB) has decided that it will no longer have wastewater from its various processes collected by a waste management company. Instead, the Saxon company has opted to deploy a VACUDEST vacuum distillation system from H2O GmbH. The resulting annual savings amount to €40,000. What impression has the new system for zero liquid discharge production left at KBB GmbH? An interview with Michael Stitterich, Production Engineer with a focus on factory planning and technical cleanliness at KBB GmbH.
Mr Stitterich, what can you tell us about Kompressorenbau Bannewitz GmbH? What are its core areas of business?
We have produced exhaust-gas turbochargers for diesel and gas engines for over 60 years now. We are located in Bannewitz, Saxony, not far from Dresden, and we manufacture products for ship, locomotive and industrial engines. Since 1953, we have manufactured over 50,000 KBB turbochargers, which are used to reduce the pollution content in exhaust gases and increase engine efficiency. Our 170 employees supply a global network of 41 independent service stations for the development, production and maintenance of exhaust-gas turbochargers.
This must mean that your production processes produce a wide range of industrial wastewaters, with different compositions?
That’s right. Cooling lubricant emulsions accrue from turning machines and machining centres on our production line. This accounts for around two-thirds of the total volume. The remaining third consists of used washing and rinsing water.
This process water accumulates in roughly equal portions from our single chamber washing systems used during production and from the ultrasonic washing plants for turbocharger maintenance. For this reason, it was also important for us to find a good integrated solution to deal with all of these wastewater streams.
What are the main reasons behind your decision to treat your process wastewater instead of dispose of it?
Our design is driven by two primary concerns. Previously, we disposed of all our wastewater. Using the VACUDEST system allowed us to achieve savings of around €40,000 annually on our relatively high disposal costs.
Our calculations showed an amortisation period of only 2.3 years for the entire VACUDEST system.
The second reason behind our decision was a desire to make a positive contribution to the environment. We recycle the distillate to prepare the cooling lubricants and washing and rinsing water. As a result, we barely need fresh water anymore.
Thanks to VACUDEST, we now dispose of less than ten per cent of the wastewater as a concentrate. Our disposal partner is therefore needed less often, thereby also reducing both traffic congestion and CO2 emissions.
Why did you opt for vacuum distillation?
Chemical/physical separation requires additional chemicals and recycling the purified wastewater is questionable. Vacuum distillation really scores points here. It reliably treats all of our many diverse wastewater streams, so that the water can be recycled in our processes.
Why did you specifically decide on a VACUDEST evaporator?
Above and beyond the benefits I already mentioned, the VACUDEST system is a convincing choice due to its ease of use.
The equipment is fully automatic and can even run over the weekend, while daily maintenance work takes less than half an hour. We also had a generally positive impression of H2O as a company. Their interaction with our company was very professional, which played an important role in the decision-making process.
Our calculations showed an amortisation period of only 2.3 years for the entire VACUDEST system.
How satisfied are you with the progression of the project and your new wastewater treatment system?
Very satisfied. Everything went well across all project phases, from planning right through to execution. At the outset, the wastewater sampling carried out in the H2O application centre for zero liquid discharge production was very helpful to evaluate the economic viability of the project. The discussion with the current operator of a system as part of a visit to a reference facility was very informative for us. It helped convince us that this was the right decision.
Let me say this about our initial experiences with the system:
In the initial stage, the training provided by H2O at our site got us familiar with the system quite quickly. The control systems are self-explanatory and require a minimal amount of effort to operate. Personally, I appreciated direct contact with the service technician, since I was able to later clarify any remaining questions with him directly.
In general, we always had a contact person and our special request for a ‘traffic light filling level indicator’ was no problem.
Case Study 2
Evaporation stills fear of chelates and heavy metals
Zinc nickel plating is the state of the art corrosion protection method for stainless steel. In the automotive industry as well as in the mining and in the production of windmills it replaces old processes like alkaline zinc plating for instance. The electrolytes used in zinc nickelplating contain highly concentrated chelating agents. This makes treatment of such industrial wastewater conventional chemical physical treatment systems very difficult.
Evaporation stills fear of chelates and heavy metals
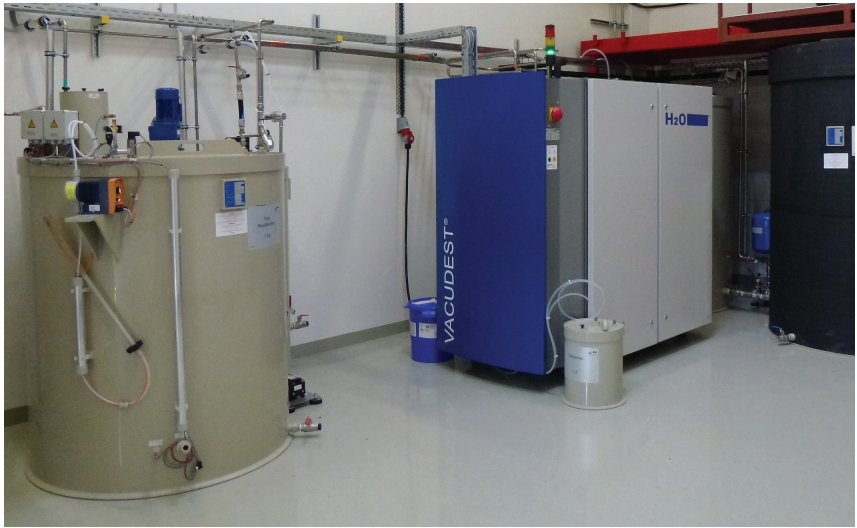
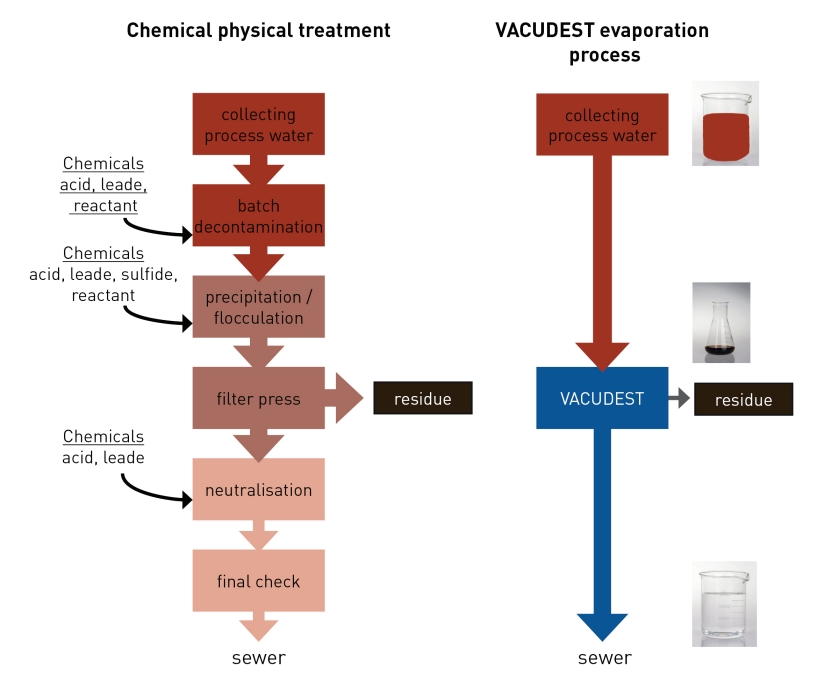
As an alternative to this oxidation and precipitation treatment evaporation has proofed to be able to separate heavy metals and chelating agents reliably. This eases treatment of waste water from zinc nickel plating. The treated water can be recycled as process water to several process steps, creating a zero liquid discharge production. Difficult treatment of wastewater containing chelating agents or cyanides.
The treatment of zinc nickel plating waste water using conventional chemical physical methods in high chemicals consumption and work load for operators. Precipitation of heavy metals is very difficult. Precipitation using sulfides frees chelating agents These free chelating agents immediately bind other metals. Thus limits regarding heavy metal concentrations are difficult to meet.
Depending on the anolyt system applied chelating agents free cyanides when being decomposed. Chelating agents as well as cyanides can be decomposed by oxidation, and filtration; however this process step increases cost because of chemical and additional operator work load and reduces process reliability.
Low investment cost – high operation cost
Investment costs for conventional zinc nickel plating wastewater treatment system are rather low. High chemicals consumption and high operator work load result in high operation cost, especially if the wastewater composition varies. In addition authorities require reporting regarding compliance with disposal limits.
Modern process: vacuum evaporation
An alternative is thermal treatment of the zinc nickel wastewater. Vacuum evaporation relies the principle of difference in boiling points. When evaporating industrial wastewater substances having higher boiling points than water (oil, fat, heavy metal salts) remain in the evaporation residue, like for instance lime and salts precipitate in a tea pot which has been forgotten on the oven. Industrial waste water from zinc nickel plating is evaporated under vacuum of about 650 mbar at a temperature of about 86 °C. The emerging steam, free of heavy metals and salts, is compressed in a roots pump to atmospheric pressure. During compression the steam is heated to about 120 °C. This super-heated steam is then used to provide energy to the evaporation process.
No costs for iron salts, milk of lime, flocculation agents and other chemicals Costs for chemical consumption are lower. Less manual work to operate the vacuum evaporation system Maintenance and operation work load is by about 70 % lower. Lower costs for the treatment of municipal fresh water to ensure quality requirements to the rinsing water in the zinc process Treated water from evaporation can be recycled to the process creating a zero liquid discharge production
Compared to atmospherical evaporation this energy recycling energy consumption by 95 % Compared to pump evaporation systems this energy recycling
reduces consumption by 60%. The treated water can be reused as process water in the plating process. It can replace demineralized municipal water. To ensure quality requirements polishing using on exchanger might be necessary. This would definitely ensure conductivity below 10 µS/cm. Certainly the treated water can be disposed of into the public sewer system as well.
Comply with legal limits despite chelating agents!
It is a horror for every production manager. Surprisingly authorities check compliance with legal limits and proofs that nickel limits have been markedly exceeded. It has passed through the wastewater treatment because it is by chelating agents. This immediately creates trouble and high workload.
Industrial wastewater treatment is not production related, thus no one really wants to take care of it. Treatment of such waste water is an non profit area which has to work reliably without putting too much effort into it.
Due to being a physical process vacuum evaporation gains points against conventional chemical physical treatment methods regarding process reliability. Heavy metals and salts are separated reliably. There is no risk to allow heavy metals to stay in the water due to using a wrong flocculating agent or due to adjusting the pH to a wrong value. If even the treated water is recycled a zero liquid discharge production is created and no disposal limits have to be kept any more.
Operation cost: Chemicals or energy?
No matter which process is used, vacuum evaporation or chemical physical treatment, operation costs cannot be prevented. Main part of the operation cot of modern vacuum evaporation systems are the electricity costs. Many people regard this technology as being a energy guzzler. This might be true for conventional systems. Modern vacuum distillation systems use 35 to 70 kWh/ m³ of wastewater, depending on capacity. Certainly this is still more than the energy consumption of conventional precipitation and flocculation technology, but there are other factors reducing operation costs drastically.
Operation experience at Compte Galvanotechnik
The meduim sized company, founded in 1836 in Sulingen, Northern Germany, today is a well respected coating specialist to the automotive and machine building industry. In the existing waste water treatment system it was not possible to treat waste water from zinc nickel plating, since compliance with legal limits could not be achieved.
Mr. Hölzchen, environmental manager of Compte Galvanotechnik, studied several different possibilities to treat this water ensuring process reliability. In the Application center of H2O GmbH it could be proofed that vacuum evaporation system fulfills these requirements. Results regarding operation cost, evaporation rate and quality of treated water convinced Compte Galvanotechnik to invest in VACUDEST from H2O in 2011. Mr. Hölzchen ensures that today the treatment systems works reliably and complies with all Compte Galvanotechenik requirements.
The lowest investment costs are not of biggest importance, optimized operation costs ensure tomorrows earnings!
Decision in favor of an industrial waste water treatment system is not an easy task. Many different factors have to be looked at very carefully. But even in times of tight budgets one can proof that low investment cost is not the most important factor. Operation cost, operation work load and independence from compliance with legal limits have bigger impact on the life cycle cost of a treatment system for industrial wastewater.