The solution for wastewater containing mould release agents from the aluminium die-casting process
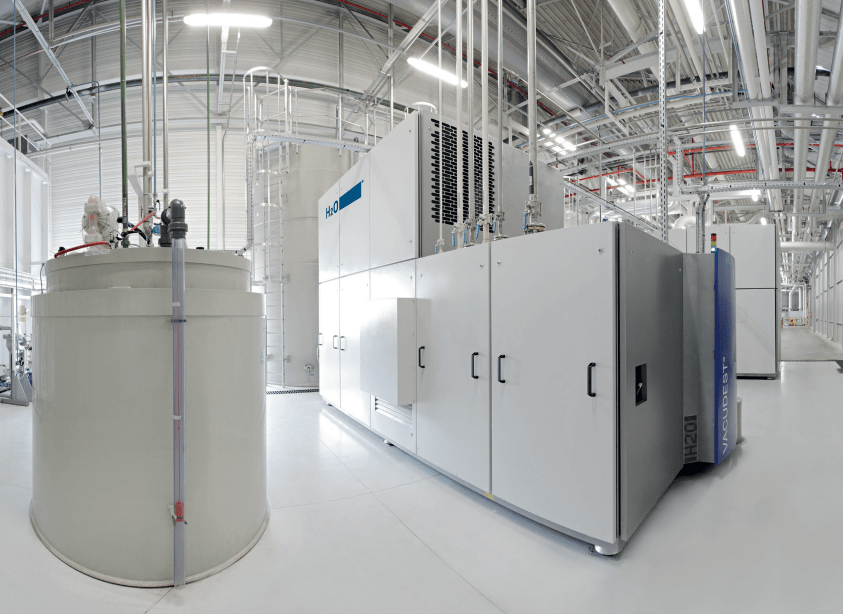
The solution for wastewater containing mould release agents from the aluminium die-casting process
Within the die-casting process, release agents are essential additives for avoiding disruptions to the production process and ensuring the quality of the parts that are produced. The used release agents, which are dissolved or emulsified in the operational wastewater from the foundry, must not be introduced into the public sewerage system.
They are normally disposed by certified specialist companies together with other commercial waste. Depending on the amount of wastewater produced, this costs far in excess of 100,000 euros per annum. A cost reduction of more than 100,000 euros per year is realistic.
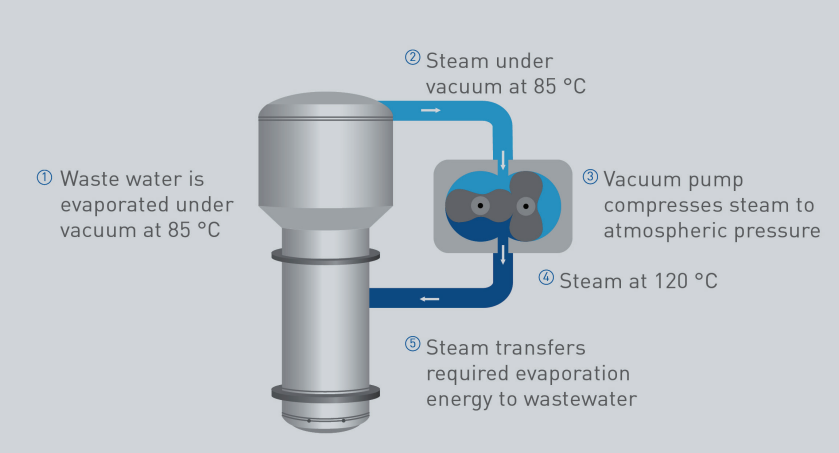
The alternative to disposal is in-house wastewater treatment. This process removes environmentally hazardous substances from the wastewater so that it can ultimately be introduced into the public sewerage system. For many years, leading die-casters have used
vacuum distillation systems for this purpose. These systems have established themselves as the safest and most efficient method. The method is based on the simple principle of separating substances on the basis of their boiling point difference.
The foundry wastewater is evaporated. All substances with a boiling point higher than water remain in the evaporation residue. This includes heavy metals and minerals, but also oils, fats, and of course, the release agents. Because the water content is evaporated, the volume of the residue from the evaporation is reduced to 0.5 to 5 percent of the original wastewater volume. This evaporation residue is then disposed by the certified specialist at a fraction of the original cost. Because of the disposal cost reduction, the investment in the treatment system will pay for itself in less than two years in the majority of cases.
The energy efficiency of 95 percent ensures that the operating costs are kept extremely low
Once branded as energy guzzlers, modern evaporators are extremely economical. The energy of the steam that is produced is led back to the vacuum distillation system. As a result, no external heating energy is required. The energy efficiency in comparison with atmospheric evaporation is now 95 per cent. The operating costs of evaporators are therefore much lower than those of other treatment methods, even though energy prices are on the increase.
Reliable and safe process
Not all industrial wastewater is industrial wastewater from the outset. This also applies to the operational wastewater from the aluminium die-casting process. Depending on the release agents used and the other impurities in the wastewater, a suitable treatment process must be designed. H2O GmbH from Steinen, Germany, a leading manufacturer of vacuum distillation systems, has analysed the requirements for wastewater treatment in die-casting and developed a system that is tailored to it. As well as efficiency with regard to operational costs, a great deal of importance was also placed on process reliability. The intention was to come up with a simple, straightforward system that did not detract from the foundry’s main task of production.
Reliable adherence to discharge limits
The wastewater from aluminium die-casting often has a pH value of less than seven, and is therefore slightly corrosive. To avoid damage to the evaporator and comply with statutory discharge limits for the treated water, the water first had to be neutralised using conventional evaporators. H2O GmbH’s Dest control technology measures the pH value in the distillate and doses lye directly into the evaporator to adjust the pH. Continuous neutralisation upstream of the evaporator is therefore no longer required.
The distillate of conventional evaporators may not be discharged directly into the sewerage system, because the limit value for hydrocarbons is not adhered to. The treated water needs to be post-treated via adsorbers, activated carbon filters or membrane systems before it can be allowed to enter the sewer. This is why H2O GmbH has developed the pioneering ClearCat condensation unit. It ensures that the distillate reliably adheres to the discharge limit for hydrocarbons. It also means that another process step can be omitted completely.
The elimination of two process steps means that operating costs are reduced and there is less risk of component failure. At the same time the cost of maintenance and repair decreases, and less space is required for the treatment system. The user is therefore reducing operating costs, increasing system availability and saving valuable space for production. Sustainable production, for a clean environment. The treated water reliably meets all statutory
discharge limits. It also has extremely low conductivity and is free of hardening components. It therefore. makes sense to reuse the water in certain production processes, such as makeup water for cooling towers, soil washing water, or rinsing water for slide grinding and part cleaning processes. In an ideal case,
production can be made completely wastewater-free.