Sustainable and economical. MAN Nuremberg cleans industrial wastewater 3 times better
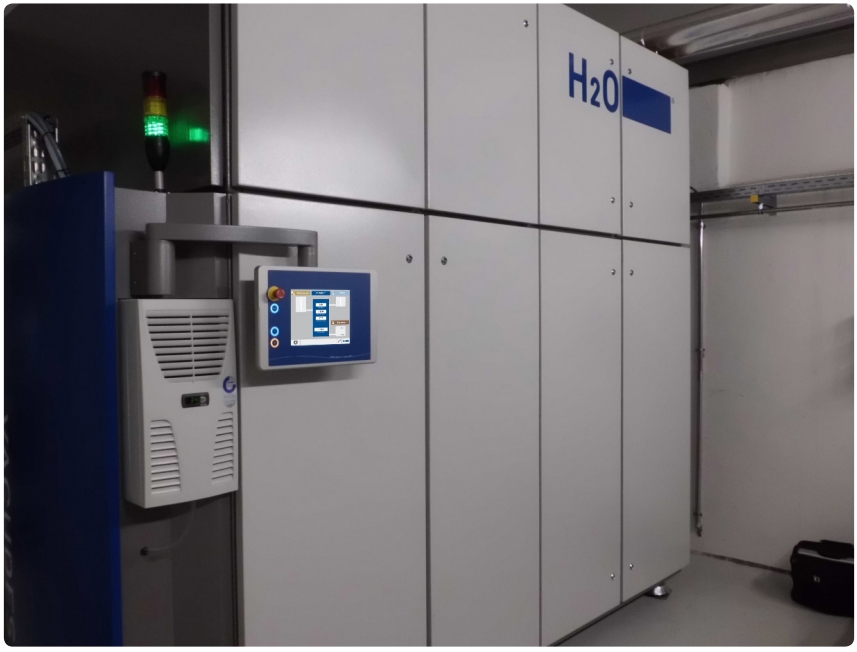
Sustainable and economical. MAN Nuremberg cleans industrial wastewater 3 times better
Within the MAN Truck & Bus Group, the MAN site in Nuremberg is the international competence centre for the development, production and sale of diesel and gas engines with an output range from 37 kW to 1,397 kW (50 hp to 1,900 hp).
MAN engines have always been a reliable source of power for the Group‘s own MAN and NEOPLAN trucks and buses. In addition, they also go to work with all their energy in road and rail vehicles, yachts and work ships, power generators and combined heat and power units, construction and agricultural machinery.
During the production of many of the required components, approx. 4,000 m³ of cooling lubricant emulsions and parts washing water are produced annually. These were previously separated using an ultra-filtration plant and the treated wastewater was then discharged into the public sewer system. Here MAN was striving for a more environmentally friendly solution. The company decided to optimise the process and to ensure a sustainable treatment of the process water produced. For example, a call for tenders was launched in search of newer and more efficient methods. H2O GmbH from Steinen in Baden offered a VACUDEST vacuum distillation system individually adapted to the requirements.
The analysis of the customer‘s process water in H2O‘s own laboratory confirmed that the treatment using the vacuum distillation can be successfully performed. These results were the first step in the right direction. The quality of the results in the laboratory also exceeded the strict requirements at MAN.
Industrial wastewater | Distillate | Concen- trate | |
---|---|---|---|
Chemical oxygen demand (CSB) | 43.680 mg/t | 1.714 mg/t | |
Evaporation rate | 97.3% | 2.7% | |
Concentration Factor 1: | 36.7 |
The evaporation rate also showed the customer that he only has to dispose of 2.7 % of waste from his process water and can expect a concentration of almost 1:37. Vacuum distillation with VACUDEST is a very efficient separation process for separating high boiling impurities from industrial process water. Nevertheless, certain physical effects prevent oils in particular from being completely separated by distillation and lead to traces in the distillate. This effect is known to all plant manufacturers and can often lead to a clouding of the distillate. Common after-treatments are based on coalescence separators and activated carbon stages. In addition to the running costs, there is also the follow-up treatment.
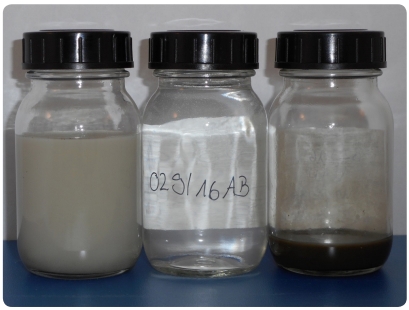
Not so with the patented H2O Clearcat system – it guarantees highest distillate quality without the use of the usual follow-up treatment and consumable materials. This additional option for the innovative VACUDEST vacuum distillation system allows the safe and efficient treatment of industrial waste water containing oil and grease in a single process step. The operating principle of the Clearcat condensation stage is based on physical and catalytic effects. Therefore, this cutting-edge technology requires neither energy nor auxiliary or operating materials.
H2O improves the quality of treated water and sets new standards. In the end, H2O also convinced the responsible employees at MAN Nuremberg.
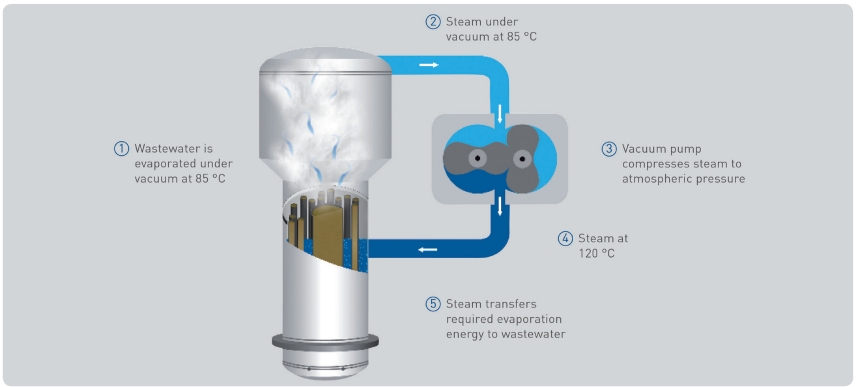
Another decisive factor for the VACUDEST plant were the lower operating costs due to the simple chemical cleaning. Everyone knows the problem with the iron or coffee machine: Hardeners in water and other impurities can occupy the heat exchanger and ensure increased energy requirements and additional expenditure for maintenance and cleaning. With vacuum evaporators, the risk is many times higher. Although chemical rinsing equipment can often delay cleaning, it can only completely replace it in a few cases. The proven Activepowerclean technology helps here:
Activepowerclean stands for a technology development that uses small (6 mm) ceramic balls for continuous heat exchanger cleaning. Due to the natural circulation of the process water in the heat exchanger, the ceramic beads are constantly “boiled along“ and clean the surface during the process. So this applies: Coating avoidance instead of coating treatment!
Mr Neumann, head of media supply at MAN, and Mr Klein, project manager at MAN, were very enthusiastic about the performance and treatment from VACUDEST and hope for many years of successful environmental protection and that MAN could decide in favour of recycling in the future.
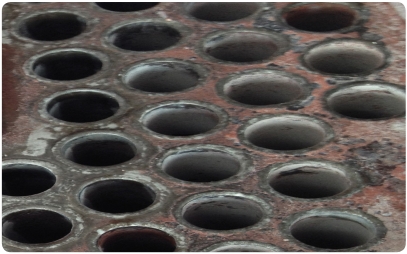
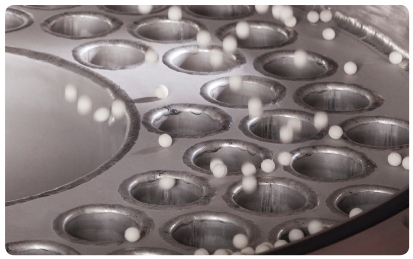
Case Study 2
Zero liquid discharge - Mubea opts for economical and future-proof evaporator technology
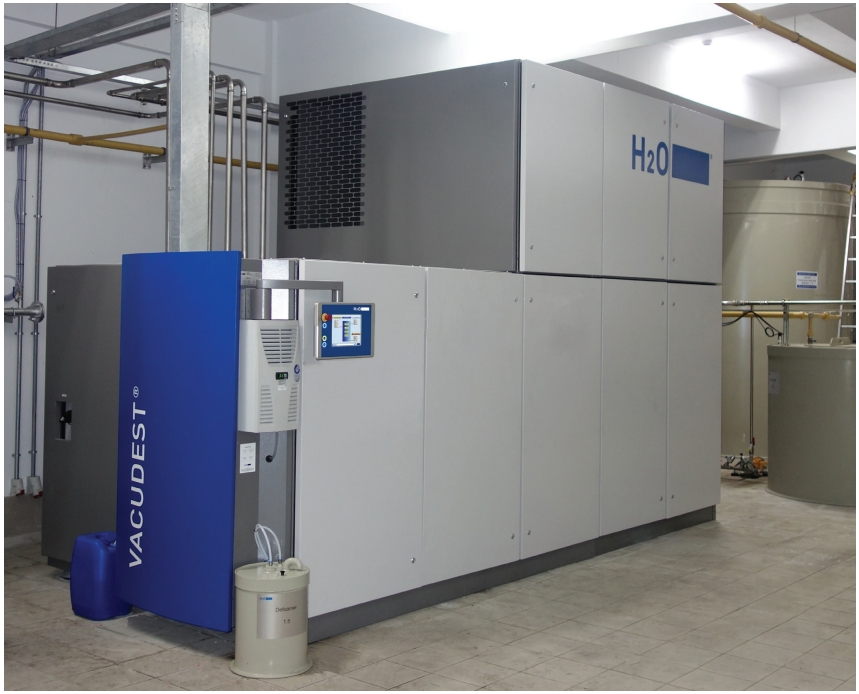
Zero liquid discharge - Mubea opts for economical and future-proof evaporator technology
Sustainable and economical – these were Mubea China’s demands for its new wastewater treatment. So the leading manufacturer of suspension springs for the automotive industry opted for an H2O vacuum distillation system.
Mubea uses water-based processes such as degreasing and zinc phosphating in its springs production, in order to improve anti-corrosion properties. The resulting wastewater contains heavy metals and phosphates and may not be discharged into the sewerage system. Particularly strict phosphate limits are in force at their Taicang site, which classical chemical/physical wastewater treatments cannot reliably meet.
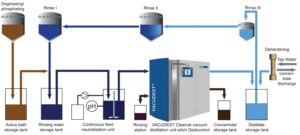
These were further exacerbated by the new GB 21900 emission standard, which came into force from 1 August 2008. As a result, only wastewater recycling through vacuum distillation proved eligible as the single technically feasible and simultaneously economical alternative.
Recycling with the VACUDEST
Using a wastewater sample from Mubea, H2O developed a suitable treatment process at its in-house Sustainable and economical – these were Mubea China’s demands for its new wastewater treatment. So the leading manufacturer of suspension springs for the automotive industry opted for an H2O vacuum distillation system. The VACUDEST XL at Mubea in China treats degreasing and zinc phosphating wastewater in an economical and sustainable manner. application centre for wastewater-free technology. Additional considerations of operating costs, and the vast savings potential from avoiding additional disposal costs, were at the forefront of the selected wastewaterfree production design.
What does the chosen technique look like in close-up? The wastewater produced is collected in a storage tank. From here, it is pumped to a neutralisation stage, in which the pH is preset to the desired value. After that, the VACUDEST treats the wastewater. The result is that the contaminants are separated into concentrate and clean, oil-free distillate suitable for reuse.
Vacuum distillation operating principle
Vacuum evaporators are based on the simple principle of separating substances according to boiling point deviations. The industrial wastewater is evaporated. All substances with a boiling point higher than water remain in the evaporation residue. This includes heavy metals, salts, oils, fats or surfactants. Because the water content is evaporated, the residue reduces to between 0.5 and 5 percent of the original wastewater volume. The rising steam, also known as vapour, is virtually free from impurities. After condensation, it can be recycled in the production process as process water. Production therefore becomes wastewater-free.
Two additional patented H2O technologies improve the distillate. The first is the dest control pH value dosing. It continuously monitors the distillate pH value and doses lye directly into the heat exchanger as required. The advantage of this is that unwanted acid components do not get into the distillate and the desired pH value remains consistently stable. Additionally, the patented H2O GmbH Clearcat module is used to give oil-free distillate. This system guarantees distillate hydrocarbon values of below 10 mg/l. After this, the crystal-clear distillate is stored in a distillate collection tank and pumped back into production for use in rinsing.
Values in distillate
Conductivity: 50 µS/cm Total hydrocarbons: 3.3 mg/l
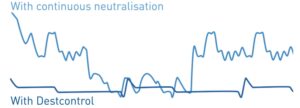
Advantages of recycling with VACUDEST evaporator
- Good distillate quality allows reuse in rinsing processes
- Saves fresh water
- Cost savings from freshwater desalination, as the distillate is salt-free
- Vastly reduced disposal costs
- Secure, fully automated process
- High energy efficiency through advanced vapour compressor technology
- Simple system operation via integrated Vacutouchcontrol
Experiences at Mubea
The quality of the produced distillate and the entire process have fully met the high expectations at Mubea. Mario Reinhold, technical manager at Mubea Taicang, is delighted: “The vacuum distillation system helps us to save fresh water and thus protect our environment. The evaporator is extremely reliable and, thanks to water recycling, we have been able to significantly reduce our operating costs.”
Vacuum distillation operating principle
Vacuum evaporators are based on the simple principle of separating substances according to boiling point deviations. The industrial wastewater is evaporated. All substances with a boiling point higher than water remain in the evaporation residue. This includes heavy metals, salts, oils, fats or surfactants. Because the water content is evaporated, the residue reduces to between 0.5 and 5 percent of the original wastewater volume. The rising steam, also known as vapour, is virtually free from impurities. After condensation, it can be recycled in the production process as process water. Production therefore becomes wastewater-free.
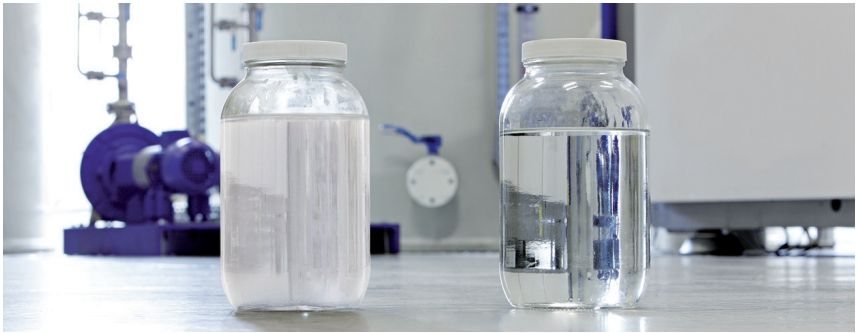