Zero wastewater discharge in rotogravure cylinder processing
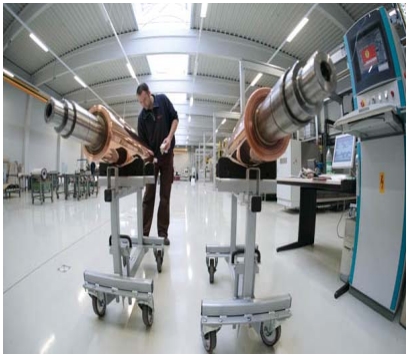
Zero wastewater discharge in rotogravure cylinder processing
The production of rotogravure cylinders for the printing industry combines different galvanic and mechanical manufacturing steps. Several of these processing steps, i.e. mechanical or laser gravure, degreasing and galvanic plating with copper, chrome or nickel are producing waste water, highly polluted with heavy metals, acids and surfactants. Evaporation by VACUDEST vacuum distillation plants has proven to be a feasible alternative to destruction or chemical-physical treatment of such water.
VACUDEST in the packaging industry: The German company 4Packaging in Dissen, producing rotogravure cylinders i.e. for Dr. Oetker, Gerolsteiner, Jacobs, Kraft or Tesa, was one of the first companies which invested in a modern process water treatment based on VACUDEST technology.
Mr. Jürgen Möller, managing director of 4Packaging has long been looking for a suitable process for treating the increasing volume of galvanic process waters. Because of the high load of pollutants, the waste water cannot be disposed of into the public sewer without
treatment.
Due to high amounts of waste water disposal through a destruction company proofed to be too costly, thus a suitable processing method allowing zero discharge had to be found. Thus 4Packaging compared several technologies available on the market.
Distillation or conventional chemical physical treatment?
A very common process in galvanic industry is the chemical-physical treatment of the process waters. The waste water is treated by acid and leach, and with additional chemicals like lime, iron salts and flocculation coagulants. Pollutants are separated from the water by filtration. Thet reated water is disposed of into the public sewer. This filter cake is disposed of through destruction companies. The big advantage of this technology are low investment cost; however the costs for chemicals and human labour involved are very high. In addition, the treated water contains a lot of neutral salts and can not be re-used, it must be disposed of into the public sewer. Legal limits for heavy metals or floured surfactants are often very strict and must be monitored and reported to the authorities frequently. In vacuum distillation plants the process water is evaporated. Pollutants stay in the small amount of concentrate, which is disposed of through destruction companies. The distillate is virtually free of salts and can be recycled in the process. Chemicals are only consumed if the feed pH needs to be adjusted prior to distillation. The system runs fully automatic and needs only little supervision. Overall operation cost are very low and feasibility is better compared to chemical-physical treatment.
Customized VACUDEST system for rotogravure cylinder processing
Different evaporation systems are available on the market. Feasibility comparison favours direct vapour compression evaporators over heat pump evaporators since electricity consumption is about one third only. One main reason for 4Packaging to decide in favour of a VACUDEST vacuum distillation plant was the customized plants offered by H2O. After careful process analysis the evaporator was equipped with several features to fulfil the special requirements in the rotogravure cylinder processing.
VACUDEST for rotogravure cylinder processing
Since rinsing water and active bath from degreasing steps need to be processed the feed to the VACUDEST contains hydrocarbons. Thus the evaporator was equipped with the innovative Clearcat technology to remove such hydrocarbons reliably. Due to pH adjustment in the neutralisation tank metal hydroxides will precipitate. The Activepowerclean technology prevents fouling due to these metal hydroxides. Thus better heat transfer is guaranteed. Results are lower total energy consumption and increased evaporation rate to minimize concentrate volumes, thus destruction cost are reduced.
End of cycle detection is done automatically by measuring the pressure in the VACUDEST vacuum distillation plant. Thus the optimal concentration factor is reached, independent from fluctuations in the feed water composition. This even active bath can be processed without need to change process parameters. The distillate leaving the evaporator is free of salts, and heavy metals. It has a conductivity of less than 20µS/cm and is virtually free of oils (less than 10 mg/L hydrocarbons) and surfactants. Typically a evaporation rate of 97% is reached when processing water from rotogravure cylinder processing, thus 1,000 l feed water would produce about 30 l concentrate to be disposed of. Further reduction of conductivity is reached by treatment of the distillate in an ion exchanger. Water losses are compensated by tapped water treated in a R/O system.
Turn Key project for 4Packaging Technical reliability was very important for 4Packagings decision in favour of a VACUDEST vacuum distillation plant. Jürgen Möller wanted one reliable partner being responsible for the complete water treatment system, thus he asked H2O for a turn key quotation including ion exchanger, R/O system, all related tanks, pumps and pipes. A maintenance contract guarantees a response time of less than 24 h in case any service is required. The complete package offered from H2O, engineering of the process water treatment system, supply, installation and start up of the plant, operator training and the customer service agreement ensures 4Packaging optimal operational availability. Since production depends on reliability of the water treatment system this was one of the most important requirement from 4Packaging.
Best quality of the recycled water Jürgen Möller stated: “The new VACUDEST vacuum distillation plant saves money due to lower operation cost compared to the old chemical-physical treatment plant. We have zero discharge production facilities enabling recycling of the distillate into the process.
We can save even more cost since almost no fresh water and fresh water conditioning is needed any more. For
our new production lines, we decided to invest in a VACUDEST system again. The technology is proven and the customer service of H2O can serve as an
example.
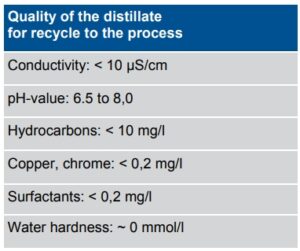
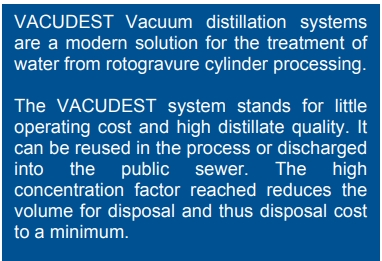